An AFC Chain Management Strategy Extends Life and Prevents Unplanned Downtime
Mining chain can make or break an operation. While most longwall mines use 42 mm chain or above on their armoured face conveyors (AFCs), many mines are running 48-mm and some are running chain as large as 65 mm. The larger diameters can extended chain life. Longwall operators often expect to exceed 11 million tons with the 48-mm sizes and as much as 20 million tons with the 65-mm sizes before the chain is taken out of commission. Chain in these larger sizes is expensive but worth it if an entire panel or two can be mined without a shutdown due to chain failure. But, if a chain break occurs due to mis-management, mishandling, improper monitoring, or due to environmental conditions that can cause stress corrosion cracking (SCC), the mine faces major problems. In this situation, the price paid for that chain becomes moot.
If a longwall operator is not running the best chain possible for the conditions at the mine, one unplanned shutdown could easily erase any cost savings garnered during the purchase process. So what should a longwall operator do? They should pay close attention to the site-specific conditions and choose a chain carefully. After the chain is purchased, they need to spend additional time and money necessary to properly manage the investment. This can pay significant dividends.
Heat treatment can increase chain strength, reduce its brittleness, relieve internal stresses, increase wear resistance, or to improve the chain’s machinability. Heat treating has become a fine art form and varies from manufacturer to manufacturer. The aim is to obtain a balance of metal properties to best suit the products function. Differentially hardened chain is one of the more sophisticated techniques used by Parsons Chain where the crown of the chain link remains hard to resist wear and the legs if the links are softer in increase toughness and ductility in service.
Hardness is the ability to resist wear and is denoted by either the Brinell hardness number by the symbol HB or the Vickers hardness number (HB). The Vickers hardness scale is truly proportional, so a material of 800 HV is eight times as hard as one having a hardness of 100 HV. It thus provides a rational scale of hardness from the softest to the hardest material. For low hardness values, up to about 300, the Vickers and Brinell hardness results are approximately the same, but for higher values the Brinell results are lower due to distortion of the ball indenter.
The Charpy Impact Test is a measure of the brittleness of a material can be obtained from an impact test. The chain link is notched at the weld point on the link and placed in the path of a swinging pendulum, the energy required to fracture the specimen being measured by the reduction in the swing of the pendulum.
Most chain manufacturers save a few meters of each batch order to allow full destructive testing to take place. Full test results and certificates are normally supplied with the chain which is normally shipped in 50-m matched pairs. Elongation at test force and total elongation at fracture are also graphed during this destructive test.
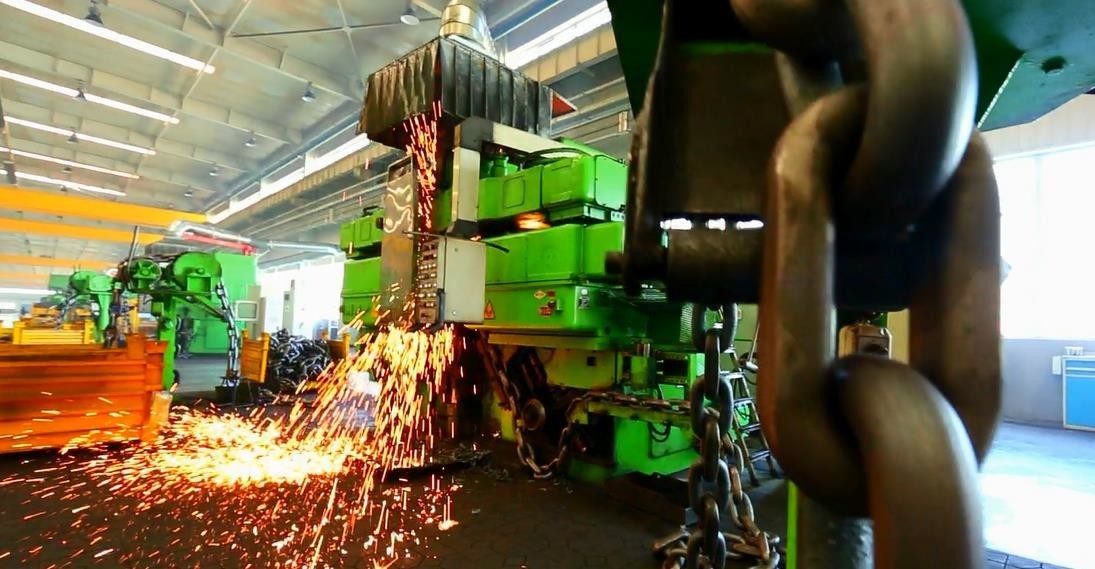
The Optimum Chain
The object is to combine all of these characteristics to create the optimum chain, which includes the following performance:
• Higher tensile strength;
• Higher resistance to inner link wear;
• High resistance to sprocket damage;
• Greater resistance to martensitic cracking;
• Improved toughness;
• Increased fatigue life; and
• Resistance to SCC.
However, there is no one perfect solution, only various compromises. A high yield point will tend to result in high residual stress, if associated with high hardness to increase wear resistance, it will also tend to decrease toughness and resistance to stress corrosion.
Manufacturers are continually striving to develop chain that will run longer and survive difficult conditions. Some manufacturers galvanize chain to deal with corrosive environments. Another option is COR-X chain, which is made from a patented vanadium, nickel, chromium, and molybdenum alloy fights SCC. What makes this solution unique is that the anti-stress corrosion properties are homogenous throughout the chain’s metallurgical structure and its effectiveness does not change as the chain wears. COR-X has proven to increase chain life substantially in corrosive environments and virtually eliminate failure due to stress corrosion. Tests have established that breaking and operating force is increased 10%. Notch impact is increased 40% and resistance to SCC is increased 350% compared to regular chain (DIN 22252).
There are instances where COR-X 48 mm chain has run 11 million tons without a chain-related failure before being decommissioned. And the initial OEM Broadband chain installation by Joy at the BHP Billiton San Juan mine ran Parsons COR-X chain manufactured in the UK, which is said to have transported up to 20 million tons from the face during its life.
Reverse Chain to Extend Chain Life
The main cause of chain wear is the movement of each vertical link rotating around its adjacent horizontal link as it enters and leaves the drive sprocket. This also leads to more wear in one plane of the links as they rotate through the sprocket, therefore one of the most effective ways to extend the life of a used chain is to rotate, or reverse it 180º to run the chain in the opposite direction. This will put “unused” surfaces of the links to work and resulting in less worn link area and that equates to longer chain life.
Uneven loading of the conveyor, due to a variety of reasons, can lead to uneven wear on the two chains causing one chain to wear faster than the other. Uneven wear or stretch in either or both of two chains as can happen with twin outboard assemblies can cause the flights to become mismatched, or out of step as they go around the drive sprocket. This can also be caused by one of the two chains becoming slack. This out of balance effect will lead to operational problems, as well as causing excessive wear and possible damage on the drive sprockets.
System Tensioning
A systematic tensioning and maintenance program is needed to ensure that after installation the wear rate of the chain is controlled with both chains elongating due to wear at a controlled and comparable rate.
Under a maintenance program, maintenance staff will measure chain wear as well as tension, replacing the chain when it has worn more than 3%. To appreciate what this degree of chain wear means in real terms, it should be remembered that on a 200-m longwall face, chain wear of 3% implies an increase in chain length of 12 m for each strand. Maintenance staff will also replace delivery and return sprockets and strippers as these become worn or damaged, examine the gearbox and oil level and make sure, at regular intervals, that bolts are tight.
There are well established methods of calculating the correct level of pretension and these prove to be a very useful guide to initial values. However, the most reliable method is to observe the chain as it leaves the drive sprocket when the AFC is operating under full load conditions. The chain should be seen to be just showing a minimum of slack (two links) as it strips from the drive sprocket. When such a level exists the pretension needs to be measured, recorded and set for the future as the operating level for that particular face. Pre-tension readings should be taken on a regular basis and the number of links removed be recorded. This will provide early warning of the onset of differential wear or excessive wear.
Bent flights must be straightened or changed without delay. They reduce the performance of the conveyor and may result in the bar dropping out of the bottom race and jumping on the sprocket causing damage to both chains, the sprocket, and the flight bars.
Longwall operators should remain on the alert for worn and damaged chain strippers as they may allow slack chain to stay in the sprocket and this may result in jamming and damage.
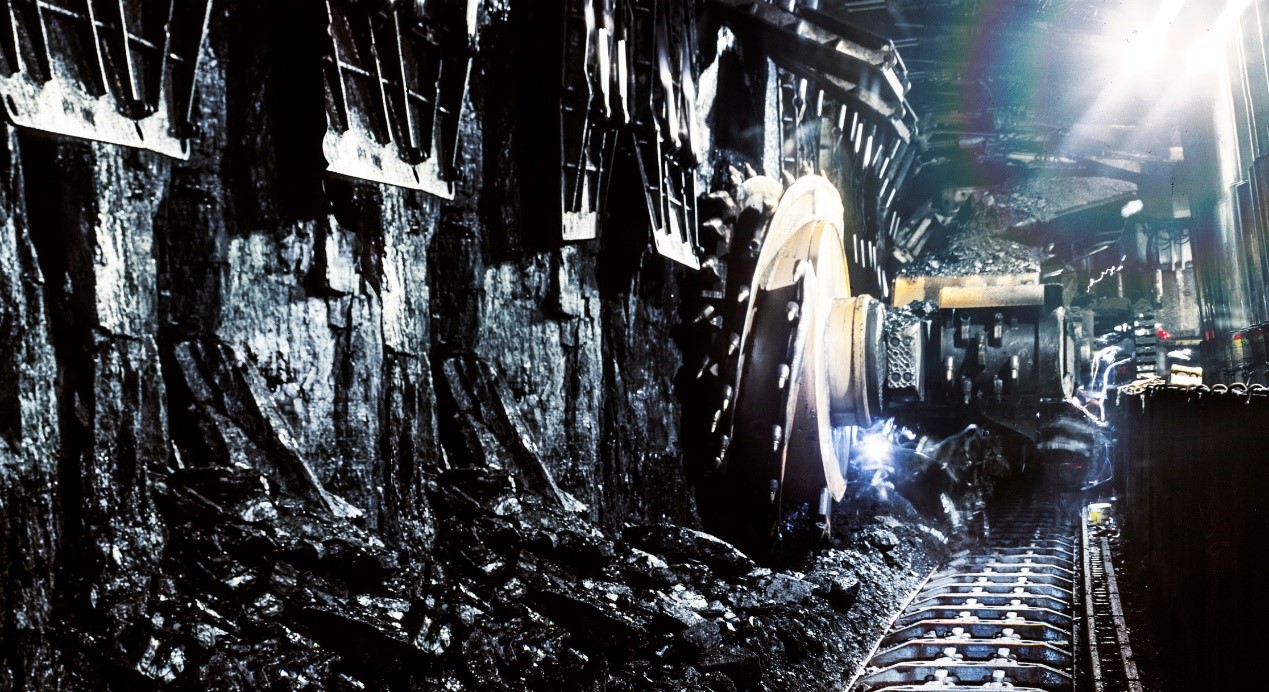
Chain Management Begins During Installation
The need for a good straight face line can’t be over emphasized. Any deviation in face alignment is likely to result in differential pretensions between face- and gob-side chains leading to uneven wear. This is more likely to occur on the newly established face as the chains run through a “bedding in” period.
Once a differential wear pattern is formed it is virtually impossible to redress. More often than not the differential continues to worsen with slack chain wearing to create more slack.
The adverse effects of running with a poor face line leading to excessive variations in side for side pretensions are illustrated by reviewing the numbers. As an example, a 1,000-ft longwall with 42-mm AFC chain that has approximately 4,000 links in each side. Accepting that interlink wear-metal removal takes place at both ends of the link. The chain has 8,000 points at which metal is worn away by interlink pressures as it’s driven and as it vibrates down the face, suffers shock loading or is effected by corrosive attack. Therefore, for every 1/1,000-inch of wear we generate 8 inches of increase in length. Any slight variation between face- and gob-side wear rates, brought about by uneven tensions, quickly multiplies to a major variation in chain lengths.
Two forgings on the sprocket at the same time could lead to undue wear of the tooth profile. This is due to the loss of positive location in the drive sprocket which allows the link to slide on the driving teeth. This sliding action cuts into the link and also increases wear rate on the sprocket teeth. Once established as a wear pattern, it can only accelerate. At the first sign of cutting of the link, the sprockets must be examined and replaced if they need to be, before the damage destroys the chain.
Chain pretension which is too high will also cause excessive wear on both chain and sprocket. Chain pretensions need to be established at values which prevent the creation of too much slack chain under full load. Such conditions will allow scraper bars to be “flicked out” and the risk of damage to the tail sprocket caused by chain bunching as it leaves the sprocket. If pretensions are set too high there are two obvious dangers: exaggerated inter link wear on the chain, and exaggerated wear on drive sprockets.
Excessive Chain Tension Can be a Killer
The common tendency is to run the chain too tight. The aim should be to regularly check the pretension and to remove slack chain by two link increments. More than two links would indicate that the chain was too slack or the removal of four links would create too high a pretension which would induce heavy interlink wear and would seriously reduce the life of the chain.
Assuming that the face alignment is good, the value of pretension in one side should not exceed the value in the other side by more than one ton. Good face management should ensure that any differential can be held to no more than two tons throughout the operating life of the chain.
The increase in length due to interlink wear (sometimes referred to wrongly as “chain stretch”) can be allowed to reach 2% and still run with new sprockets.
The degree of interlink wear is not a problem if chain and sprockets wear together thus retaining their compatibility. However, the interlink wear does result in a reduction in the chains breaking load and resistance to shock loads.
A simple method of measuring interlink wear is to use a caliper, measuring in five pitch sections and applying to the chain elongation chart. Chains would generally be considered for replacement when interlink wear exceeds 3%. Some conservative maintenance managers do not like to see their chain exceeding 2% elongation.
Good chain management starts at the installation stage. Intensive monitoring with corrections if needed during the bedding in period will help ensure a long and trouble free chain life.
(With courtesy of Ellton Longwall)
Post time: Sep-26-2022